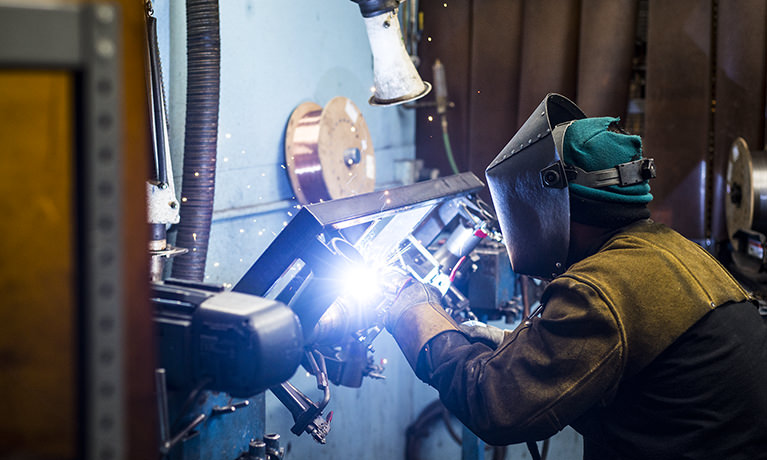
The state of California is without question the automotive aftermarket capital of America—if not, the world. It is home to countless influential entities constantly producing the world’s highest quality pieces for enthusiasts to modify their car. It also contains its fair share of racetracks as proving grounds for many of these performance manufacturers. However, it is also home to the highest population numbers in the United States. This creates quite the conundrum for tracks located near densely populated areas. Several decades ago, residents would move to be closer to the noise of the racetrack, but in the modern era, these tracks are forced to conform to their neighbors’ strict noise pollution demands.
Of these racing venues in California, circle track Sprint Car ovals were especially under attack in the early ‘80s. With residents demanding noise ordinances be put into effect, racers would have to forgo precious horsepower by muffling their exhaust systems to adhere to the lower decibel limit. Enter Ray Flugger, the founder of Flowmaster Mufflers in Kenwood, California. In 1983, Flugger designed and created the Flowmaster muffler to minimize engine noise without sacrificing performance due to the excessive backpressure normally associated with a conventional exhaust system. This led to many ‘firsts’ in automotive exhaust science, as well as patents put in place to protect the various technological advances in their products. In the 35 years since, Flowmaster has become a worldwide leader in automotive exhaust products.
We were invited to tour their manufacturing headquarters in West Sacramento, California for a unique behind-the-scenes look at how this innovative company manufactures their world-class exhaust systems.
Seemingly a world away from the 800 sq-ft barn in Santa Rosa, California that initially propelled the company, Flowmaster’s current 165,000 sq-ft manufacturing facility is now nestled inside an industrial park adjacent to the Port of West Sacramento. The company prides itself on their domestic production principles, utilizing this campus—and others across America totaling 400,000 sq-ft in total—to ensure all aspects of production are completed in-house and on United States soil.
Onto the task at hand, our guided tour through the inner-workings of its West Sacramento facility. We entered the production area by way of their clean, white office hallways. We were greeted with numerous bins of pieces involved with the manufacturing process of their mufflers.
It’s always a good sign when you see raw material on-site. Similar to other manufacturing facilities we’ve visited, the raw material is housed in spools and organized throughout the floor.
The material is then trimmed to spec for whatever piece is needed on their production schedule. In this case, it was the outer skin of one of the company’s trademark mufflers.
These trimmed pieces of raw material are then pressed to create a small lip, stamped with Flowmaster text to authenticate the piece, and formed into the shape of the muffler canister they will soon become. All of these steps being performed in one very small footprint of machines within a few feet of another.
Once the material has been stamped and formed, it receives its first weld, courtesy of one of the many automatic welders. These welding machines are used to tack-weld the ends of the metal together, to finalize its shape. Before continuing their quest in the rest of the line, these soon-to-be-canisters are stocked in large numbers.
Moving onto a different aspect of the final muffler piece, the inlets and outlets need to be specially formed depending on the application. For that, sections of stepped tubing are gathered and pressed into their desired shape using special tooling created for the corresponding end product.
Sections of straight tubing receive the same treatment, as they’re formed to the desired shape.
Alongside a few other tasks throughout production, this is an area where Flowmaster saw the opportunity to enlist the help of robotics. A single worker, trained in the processes of the robotic arm is able to oversee this automated machine capable of pumping out efficient production numbers.
Similar to the canister skin, portions of raw material are also stamped to create these caps and internal chambers.
The pieces are then pressed in machinery side-by-side, as they receive treatment that will make them usable in various Flowmaster muffler designs.
In order to create the accurate designs on these caps and chambers, Flowmaster uses dozens of proprietary jigs and tooling fit for their machinery. These are crucial to the end product, and contain different alternatives used for making even slight variations of each manufactured part.
Smaller spools of raw material were located elsewhere on the grounds. You might remember a similar machine from our tour of Eibach Springs. This machine however, is used to bend the necessary angles for use in exhaust hangers, and then trim the piece to spec.
Once bent and trimmed, they are placed into coordinated bins organized by part numbers.
Much like the hangers, numerous other aspects of the mufflers’ end construction are made in batches and stored.
So we have the canister skins, we have the inlet and outlet tubes, we have the caps, and the chambers—let’s make a muffler! The batches are collected with their various associated part numbers and assembled into build schedules in one of two methods.
The first method is automated. The company uses a system of robotic machines to seamlessly weld the internal chambers of each muffler.
The internally chambered mufflers are then passed to another robotic welder to handle the sealing of the end caps.
The other method uses one of the staff’s many trained professional welders to fuse these pieces by hand.
Once a sealed muffler is completed, it is taken in batches to a grinding station where another trained professional cleans up any burrs or harsh edges on the exterior of the product. This shower of sparks keeps the finish to the highest standard.
However, not all mufflers are created equal. Keen on continuing the founding principles behind the company, Flowmaster also manufacturers their own series of hardcore race mufflers, with more streamline designs to bring down the decibels and unleash power without sacrificing weight.
So you think you weld a lot of exhausts? Not as much as these guys.
“We use 900 pound drums of wire on our robots and hard automation. We have 21 robotic cells and 45 welding shacks. We use approximately 3600 pounds of welding wire a week, split between all the departments,” said Brian Wrathall, Flowmaster’s Production Manager and our detailed tour guide.
That’s right, an entire pallet of wire is fed through their welders on a weekly basis.
Okay, now that all of those portions of the muffler have been combined to create one solid structure, let’s make a full system. For that, the company keeps massive shelves full of different diameter and thickness tubing used to make assorted exhaust systems.
Some of this raw material is sent into a large band saw to create smaller sections like the inlet pieces we saw earlier, which is then organized into their own batches and jobs.
While the rest passes through one of the company’s handful of Horn Machine Tools CNC mandrel tube benders, which creates perfectly aligned, chassis-specific bends without sacrificing the tube’s flow.
I’d like to shed light on the different colored machinery utilized on the Flowmaster floor. You may have noticed some of the machines are blue, while some are yellow. This isn’t random, it is purposely color-coded to display that blue machines were created internally, while yellow were purchased. It is worth noting however, that many of the yellow robotics are modified in some way to coincide with Flowmaster’s needs throughout the production process.
Flowmaster’s accuracy for every job is accountable by way of their assorted jigs used in the production process. These bespoke engineered templates ensure the best fitment of the final product. They have a couple different jigs on-site to create their catalog of part numbers—just a couple.
The final step after all of these pieces have been bent, pressed, formed, welded, and organized, is to be cleaned and boxed.
Collections of part numbers are once again gathered, only this time not for the creation of a single muffler, but to consolidate into a central exhaust system ready for packaging. Workers pull from various sections of shelving and place each piece into each box one-by-one down the line until the empty boxes are full.
Which brings us to our final stop of the tour, the warehouse. Responsible for housing entire production runs of numerous part numbers, this section of the building is full of product ready to be shipped to the company’s clients all over the world.
To aid in efficiency during the packaging and palletizing process, this automated pallet wrapper envelops the stacked parcels in distinctly labeled clear wrapping. Anyone who has spent their afternoons running circles around pallets continuously unwinding cellophane to safely cover the shipment can tell you this is a sound investment—looks cool while it’s working, too!
As our tour finished, so did the manufacturing workday, and the faithful employees of Flowmaster evacuated the production floor.
These skilled craftspeople that weld, operate machinery, and work the warehouse don’t have a high turnover rate. Some of whom have been employed with the company since its headquarters was still in a barn many years ago. These individuals have grown with the company and understand it’s their direct input that creates the quality product the company is known for.
We’ll end here with the large American flag that overlooks the entry into this exhaust manufacturing giant’s production floor. By initiating the company with a strong “Made in USA” standard that has been carried through the decades, Flowmaster has produced countless innovations in exhaust technology and shows no signs of slowing down. The company was founded with dreams of making a quieter muffler with performance gains, and has in-turn changed the science behind the exhaust market. Hopefully you found this insight into their production process as rewarding as we did. Thanks for reading!